By Yiannis Ampatzidis
Vegetable growers face several serious challenges with respect to farm labor. The number of domestic farmworkers has decreased substantially. In some cases, growers are unable to fully harvest their marketable fruit. A high percentage of the remaining domestic workers are not legally authorized to work in the United States.
The costs to recruit temporary foreign agricultural guest workers through the H-2A program are quite high. Furthermore, U.S. vegetable growers face stiff competition from other countries. Mechanical harvesting systems for vegetables could simultaneously lessen the dependence on manual labor, reduce harvesting costs and improve the overall competitiveness of U.S. growers.
Strawberries in the United States are harvested every three to four days. Workers cut the berries by the stem; they do not just pull the berry. They pick only red, plump, firm and ripe berries. Harvest can last up to six to eight weeks. Picking conditions change daily, and the berry quality is affected by the local weather, pests, diseases, etc.
Strawberries will not continue to ripen once they are picked. Hence, it is challenging to develop effective strawberry harvesters for continuous and selective picking of ripe berries without damaging the fruit and plants during detachment.
Mechanical harvesters for strawberries (and specialty crops, in general) should meet several challenging requirements, including accuracy, speed, low cost and high throughput. Four main problems need to be solved in developing successful harvesting robots:
- Accurate navigation throughout the field
- Location and characterization of the fruit in the plant
- Grasping and detachment of each fruit
- Reducing damage to not only the harvested fruit, but also to the plants and flowers
Damage to a plant or flower will affect the development of new berries and decrease the overall yield of the plant throughout the season.
Recent technological advances in sensors, machine vision, mechatronics, graphical processing units and artificial intelligence (AI) have enabled the development and implementation of robotic technologies for mechanical fruit harvesting. In this article, examples of autonomous strawberry harvesters are discussed.
HARVEST CROO ROBOTICS
Harvest CROO Robotics (HCR; www.harvestcroorobotics.com) is a Florida company funded by the strawberry industry to develop an electric-powered robotic harvester. Formed in 2014, more than 70% of the U.S. strawberry production industry has invested in HCR. Since then, HCR has been developing the components necessary to automate the process of robotically picking strawberries.
HCR has developed autonomous subsystems that can work together to accomplish the overall goals of mechanized picking, sorting and packing of current strawberry varieties. High efficiency and significantly reduced costs while maintaining fruit quality can be achieved. This technology does not require growers to radically change the way they currently grow strawberries, and it can solve the urgent labor shortage problem.
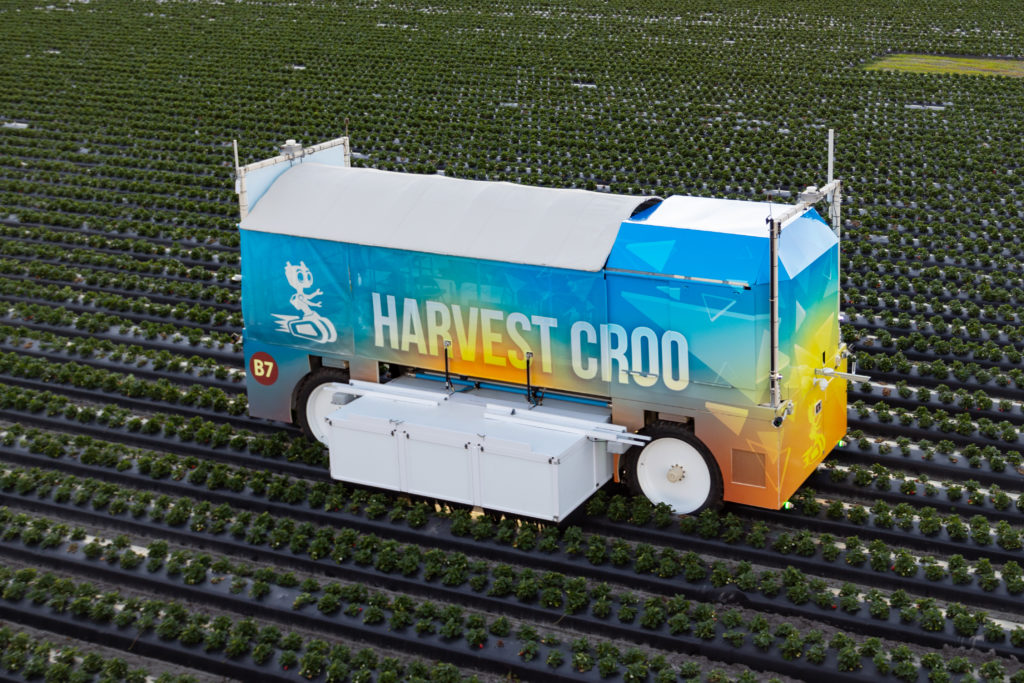
The HCR autonomous harvest platform (Figure 1) was designed to be a modular and scalable system. The current version of the harvester includes 16 independently working picking robots; four robots per row (double plant rows). It utilizes sensor fusion (e.g., light detection and ranging, multiple cameras, etc.) and AI for fully autonomous navigation to avoid obstacles (e.g., colliding with growing rows or human workers) and for picking and packing berries.
A novel mechanism for moving leaf foliage (Figure 2) was designed and utilized to pick healthy and ripe berries. HCR harvesters pick, inspect, clean (via hydro-cooling), sort (e.g., for fresh market, juice or rejects) and pack berries in the field. They are holistic pick-to-pack solutions (a combination of a harvester and packinghouse in the field). These harvesters can work night and day, seven days per week, and replace a crew of around 24 human workers.
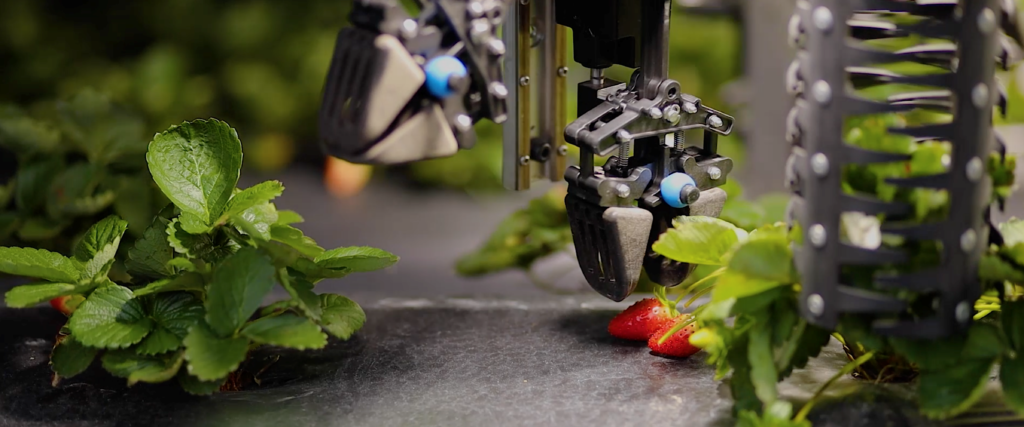
Furthermore, this harvester collects data from individual plants to help growers make informed production management and business decisions.
See youtu.be/AO1mZrB5XK8 for a video demonstration of this technology.
AGROBOT
Agrobot (agrobot.com) is a company from Spain that has developed an electric-powered and adjustable harvest robot (E-Series model). This robot utilizes machine vision and AI for navigation and picking. The adaptable platform of this robot (Figure 3) can fit into multiple farming configurations and can be used for outdoor and indoor production systems (see video at agrobot.com/e-series).
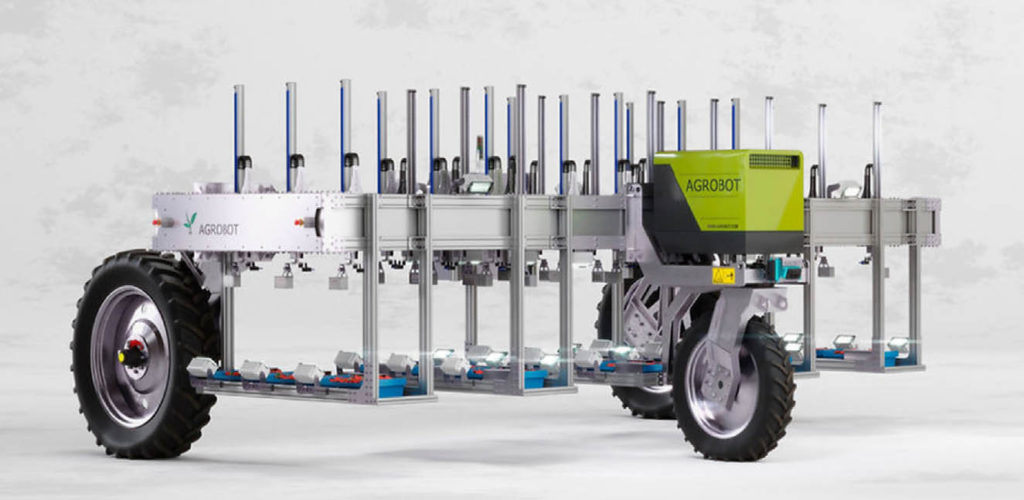
The Agrobot autonomous platform can contain up to 24 independent robotic arms for picking ripe strawberries. The system detects and locates ripe berries and then controls the movement of the robotic arm and the cutting system. The robotic arm grips and cuts the strawberry from the stem with two razor-sharp blades. It then places the berries into a container for later packing in clamshells. This technology requires a specific configuration of the growing rows (raised beds covered with plastic), including farming in single rows (not suitable with double plant rows commonly used in Florida) and potentially raising the bed’s height so the strawberries are hanging at the side of the bed (Figure 4). The harvester cannot see and pick berries covered by foliage.
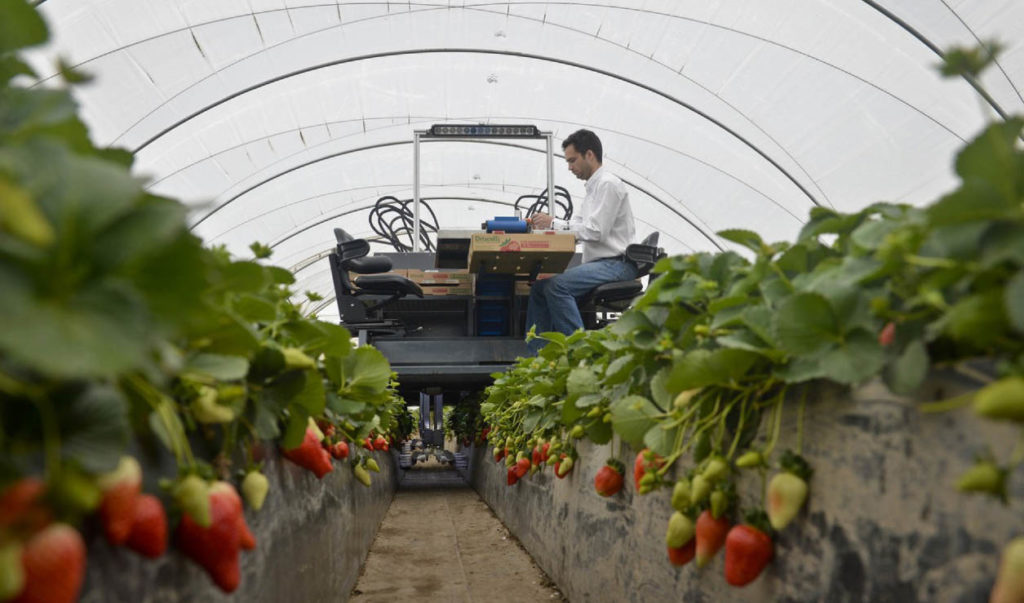
ADVANCED FARM TECHNOLOGIES
There are other prototypes under development from a few startup companies, including the TX robotic strawberry harvester developed by Advanced Farm Technologies, a company based in Davis, California. Advanced Farm Technologies (advanced.farm), founded in 2017, recently raised $25 million in investments to develop a multi-fruit robotic harvester. The TX harvester utilizes soft robotic grippers, machine vision and AI for picking ripe strawberries (see the video at advanced.farm). The company’s plan is to adapt the existing TX robotic prototype for apple harvesting, too.
Yiannis Ampatzidis is an associate professor at the University of Florida Institute of Food and Agricultural Sciences Southwest Florida Research and Education Center in Immokalee.
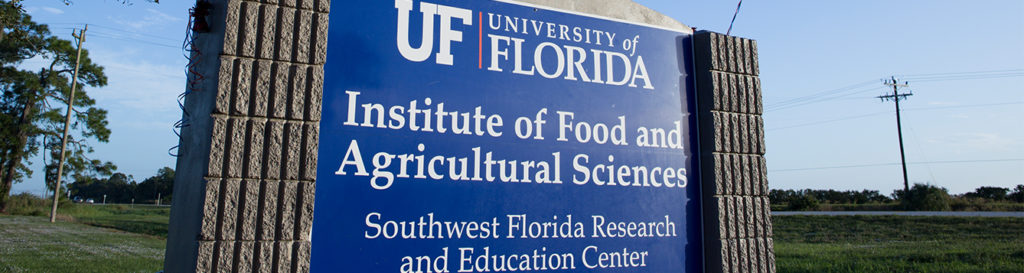