By Clint Thompson
Precision Ag innovations are needed for specialty crop producers to remain sustainable now and into the future. The only problem with that reality may be vegetable’s sensitivity.
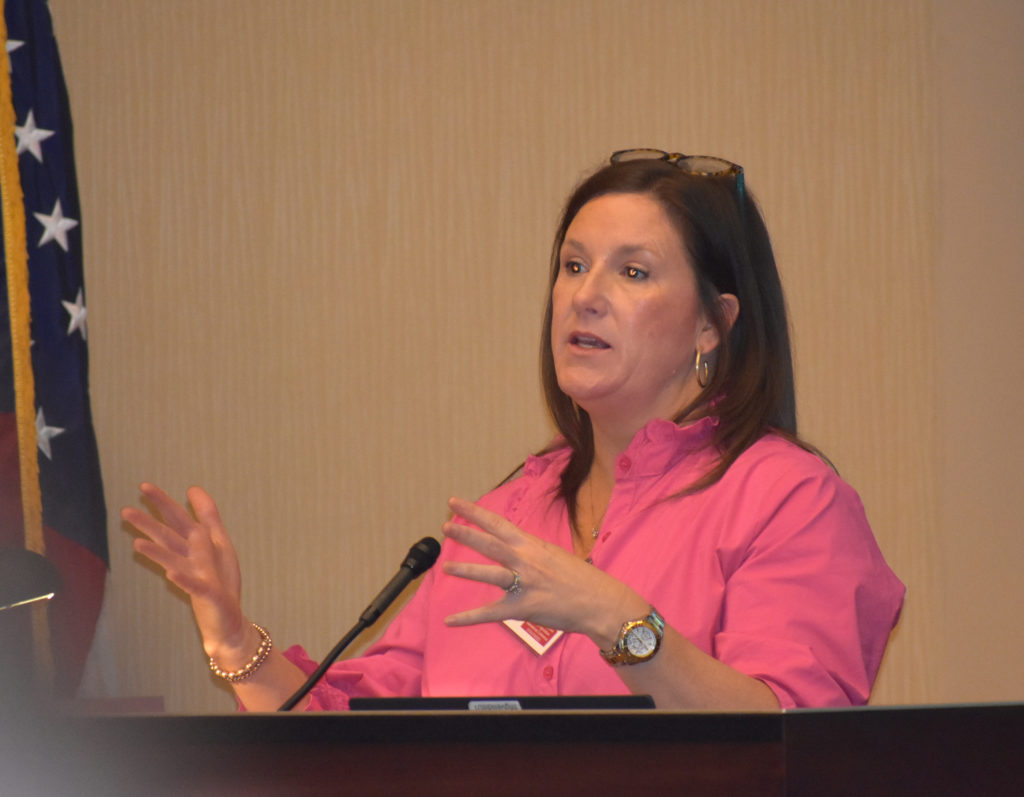
A robotic harvester may not be feasible for some of those crops because they could get damaged during harvest, believes Jessica Kirk, director of food safety and marketing at Lewis Taylor Farms in Tifton, Georgia.
“Any way that we can lower those labor costs is a win-win for us,” said Kirk, who addressed some of those concerns at the International Conference of Integrative Precision Agriculture in Athens, Georgia last week. “Our problem, as we see it, there’s currently no way to get out into the field, to make those harvests, except by hand, where that product is still marketable to grocery stores. The margins are so tight, and the fact that they want things a certain way; no bruising, no cuts, no scrapes, nothing. They want it perfect. Right now, all of the harvesting mechanisms that are in place, they damage the product too much.”
There is also the concern of knowing which crops are mature enough to be picked. Producers can look at a fruit and distinguish if it is ready to be harvested or not. Machine harvesters are not able to make that distinction.
“If they go onto a pepper plant, we would want that harvester to be able to know, this one is ripe but this one is not. You don’t want to lose the whole bush or the whole plant in one harvest. There are things out there now that do it for blueberry growers. But when they do it, it gets everything. It’s not just getting the ripe blueberries, it’s getting all of it, and you lose a lot in the process,” Kirk said.
There are some elements of precision ag that could benefit specialty crop farmers in packing facilities.
“If we could develop something within our packing facility that would meet food safety standards where we could get things more quickly through our packing lines, use less people; maybe have sensors to detect color, size instead of having to use people, that would help a lot,” Kirk said. “Especially in our greenhouse operations, there are things that are already there that just aren’t manufactured for a greenhouse operation. It could save us ton of man hours, lots of money and lots of overhead costs.”
She said that approximately 55% to 60% of Lewis Taylor Farms’ input costs is tied up with labor expenses. This includes the AEWR (adverse effect wage rate), housing, transportation, visa costs and doctor bills.