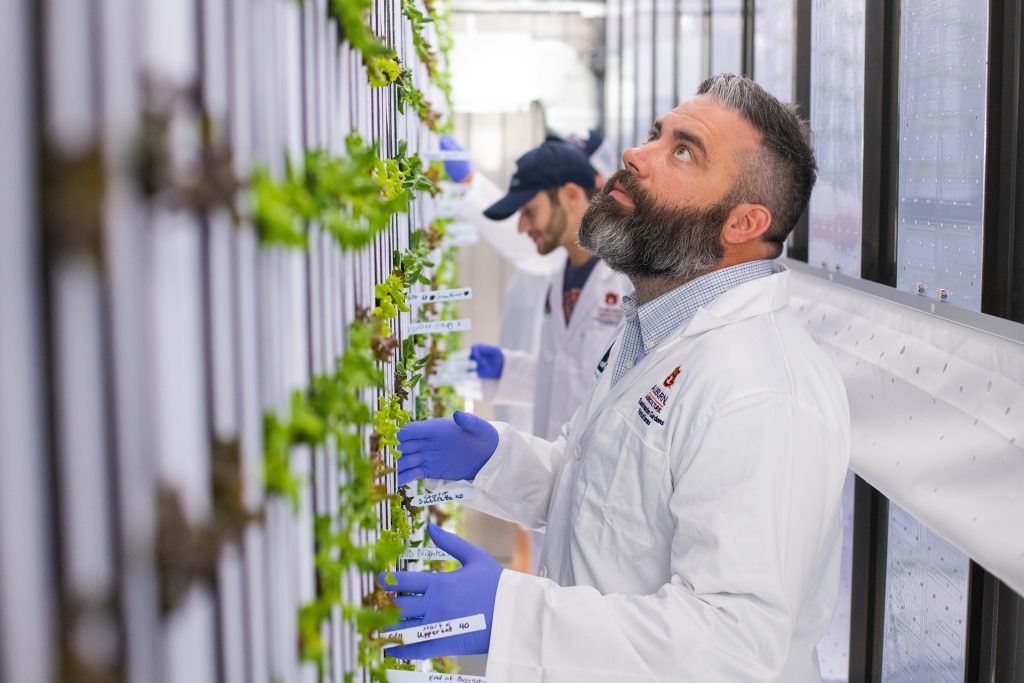
By Clint Thompson
The Auburn University College of Agriculture is using vertical farming to provide certain produce for its students year-round. Auburn students are helping to grow food for Auburn students.
This unique way of farming doesn’t involve a field or a greenhouse but a shipping container. The same container used on tractor-trailer trucks uses LED lights to provide the necessary light energy for the crops to grow. There are no windows. Scientists also control the water and nutrient supply, so the plants receive just enough but not too much.
Quicker and More Sustainable
The result is a quicker and more sustainable way to grow produce.
“It’s really very cool,” Dr. Desmond Layne, Head and Professor of the Department of Horticulture. “It is possible to grow certain crops in the container faster than if they were grown outside. The way that you can enhance the growth inside is to increase the day-length. You can run the LED lights as long as you want to. We’re currently running them about 16 hours a day so that’s a couple of extra hours of grow time per day.
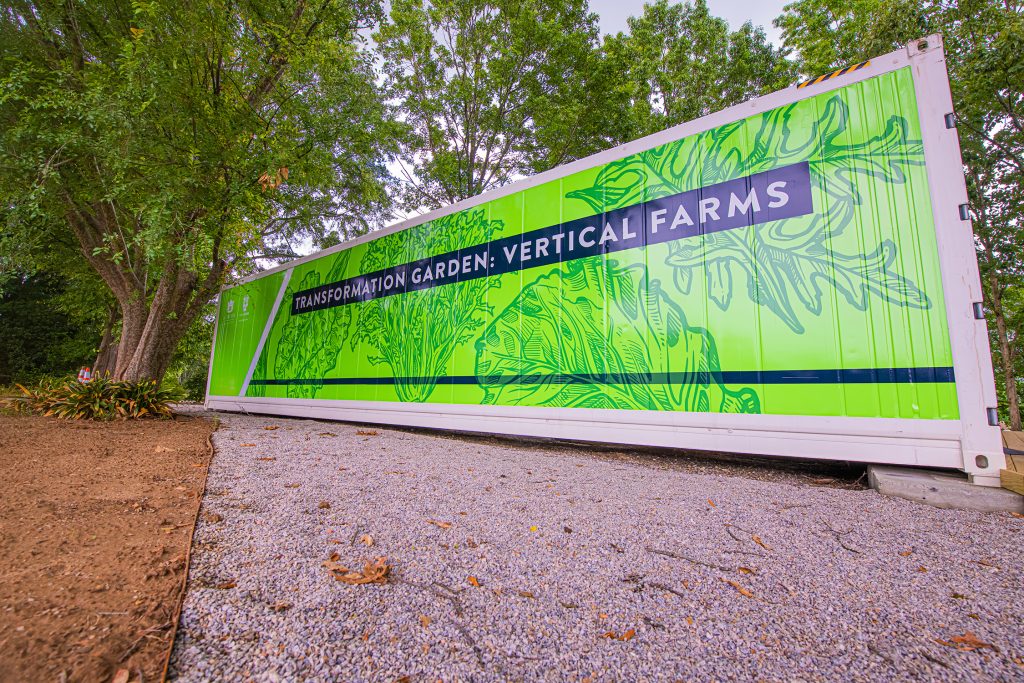
“Plus, we’re supplementing the CO2. The CO2 outside is normally about 400 parts per million. We’re increasing it in there to about 1,000 parts per million, so the plants can do more photosynthesis. With a higher CO2 and longer day-length, the plants can grow more in a 24-hour cycle.”
The Process
For example, lettuce seed is sown in plugs in the container until it is about two weeks old. It is then transplanted to the vertical walls. After about another four weeks, mature lettuce plants are ready for harvest. Because it is a climate-controlled container, lettuce can be staggered in production and harvested year-round – no matter what the conditions are outside.
“If it’s a lettuce crop and you staggered it so you planted a quarter of the container this week and another quarter next week and so on, you could literally be harvesting 52 weeks of the year,” Layne said. “We want a continuous supply of produce going into our campus dining system. This system will enable us to do that.”
How It’s Done
Vertical farming can be implemented in one of two ways with shipping containers.
Shelves of produce can be stacked horizontally one on top of each other. With this arrangement, the array of lights is stationed above each growing shelf, and the shelves are stacked to the ceiling. Each individual shelf is illuminated with lights directly above it.
Or, the arrangement inside the container can essentially be flipped on its side, with the vertical growing walls hanging from the ceiling, comparable to gutters on the house that drain rainfall. Inside those gutters is a material to hold the plug of the transplant in place. The plant grows perpendicular to the wall of the container, growing out horizontally. In this arrangement, the light walls hang down from the ceiling as well and are pointed horizontally to the plant-growing walls.
Layne estimates that approximately 4,000 plants can be produced in a container at a given time. Growers can produce 15 times as much lettuce in a year in one of these containers compared to growing in the same space outside.
Reduced Worries
Producers also don’t have to worry about pesticides or fungicides. Because the crop is produced in a climate-controlled closed environment, there is no concern for insects or diseases. An air curtain is installed above the door to prevent insects from coming in when the door is opened or closed.
The container is ideal for growing small plants such as greens, lettuce, turnips, kale. It can be placed anywhere you have a flat, stable surface and access to water and electricity. This can be in a parking lot in a city or in a remote area. Local weather climate does not matter. Some vertical farmers have containers in Alaska, the desert and many other places.
Since the container is already insulated, the crop is also protected from the outside elements. If power supply is interrupted (e.g., because of a hurricane), a portable generator can be connected to temporarily provide the necessary electricity.
The state-of-the-art converted shipping containers were manufactured by Freight Farms, a Boston-based company operating in 45 states and 28 countries.