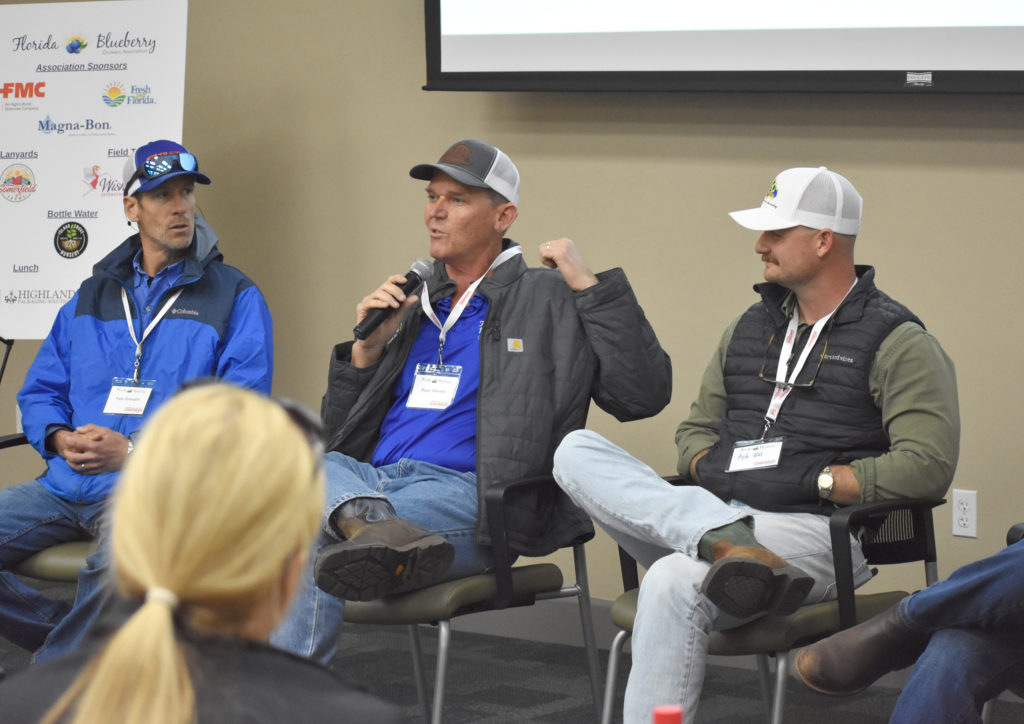
Photo by Clint Thompson
By Clint Thompson
Challenges accompany the use of machine harvesters in Florida blueberry production. But as growers who implement the technology on their farms will attest, the long-term benefits are worth the short-term headaches.
Ryan Atwood, Kyle Hill and Kyle Straughn were part of a grower panel at a Florida blueberry meeting in Citra on March 6. They agreed that there are certain caveats that factor in the success of using automated harvesters. They also stressed the need for the technology for growers to remain sustainable long-term.
“Florida has to get a better return on the fruit, and I think the only way Florida is going to stay in the game is with machine harvesting,” said Atwood, who compared Florida’s more expensive inputs to neighboring Georgia. “Georgia’s growers inherit land from their grandpa, timber it and use that money to dig canals and put in irrigation. The soil in Georgia has 6% to 8% organic matter. In Florida, we’ve got less than 1%. Southern highbush wants 4%. You’ve got to supplement with pine bark to get your organic content up, and that’s expensive. Georgia has an inherent ability to be cheaper. Even though they’ve got lower prices, they’ve got much cheaper input costs.”
Labor Pains
The main financial strain is labor costs. Florida’s specialty crop growers who use H-2A labor are saddled with a hefty price tag with the adverse effect wage rate. So, the less labor they have to rely on, the better.
“I think we can’t compete internationally without mechanical harvesting. I do believe at some point in time there will not be a commercial industry without it,” said Straughn, who has used mechanical harvesters for almost 20 years. “Luckily, it is here, and we are doing it. But it’s our only chance to compete with international labor rates.”
When to Pick
Growers must remember certain limitations that surround mechanical harvesting. When the crop can be harvested is a big one. Nighttime harvests are more common because of the decreased temperatures impacting the berry quality.
“You can machine pick during the day if the temperature is lower. On the front end of the season, you can do that,” Atwood said. “On the back end, when temperatures are up, one of the big challenges for the Rabbiteye growers in Georgia is they’re picking their fruit in June. Even though it’s a tough berry, that’s a really warm temperature. Nighttime lends itself to cooler temperatures, which leads to fruit quality being better.”
Straughn added, “You just don’t want to pick during the heat of the day with the sun baking on that berry. We try to not be out in the fields picking if it’s over 80 degrees.”
Other Limitations
It is also important to consider that not all blueberry varieties are suited for machine harvesting. Straughn and Atwood recommend Optimus and Sentinel for their locations.
Machine harvesters are also prone to break down and require maintenance. If producers choose to use mechanical harvesting, it may only comprise a small percentage of the harvested crop. Straughn uses mechanical harvesters for fresh pack at about 25%, which is double of what was harvested a couple of years ago. His farming operation has the capability to do about 50%.
Worthwhile Investment
Despite various challenges associated with machine harvesting, Atwood emphasizes the investment will be worth it.
“It’s difficult, and there’s a lot of challenges, but the economics of it are worth it. My advice to other people is you’ve got to push through it, and you’ve got to continue to make it work. It’s the way we’re going to stay in business,” Atwood said.